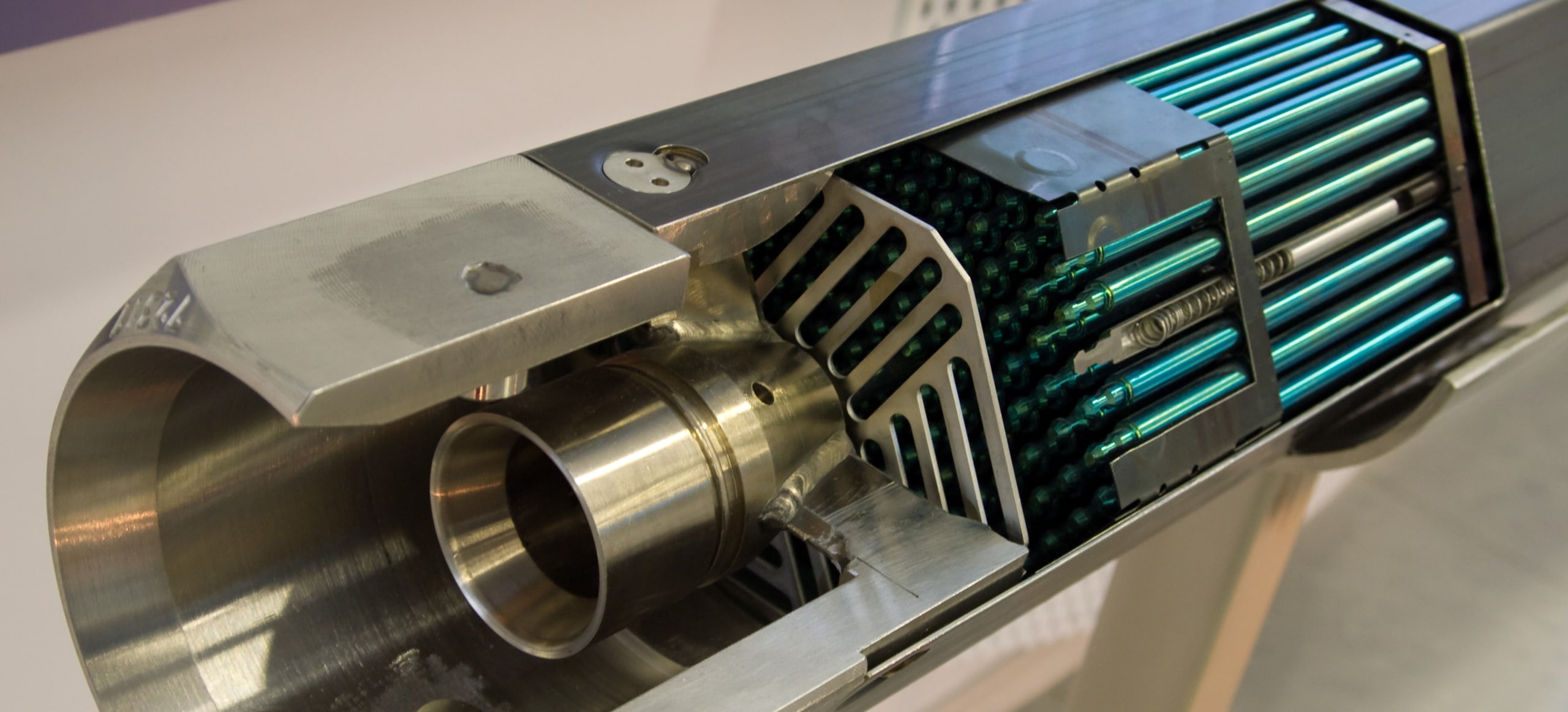
Cask Seal for Spent Nuclear Fuel Rods
Seal Master provided a cask seal for spent nuclear fuel rods.
Industry
Nuclear
Application
Sealing off and holding water in place around cask for spent fuel rods
Cross Section
G1
Location
Canada
Industry Background
Demand for dry storage casks is high all around the world. Some of the risks of storing spent fuel in storage pools can be reduced by transitioning to dry cask storage.
Project Details
Nuclear power plants are in need of an alternate way to store spent fuel, as spent fuel pools are getting full. Many nuclear plants are now moving to cask storage in which the spent fuel rods are stored. Each cask has water inside to cool down the spent fuel, and our seals help hold those water blankets in place inside the casks.
Fabric-Reinforced Inflatable Seals Customized for the Casks
Our engineering team used a custom G-1 cross section for this large seal made from EPDM for radiation and heat resistance. These casks have an incredible amount of heat and water pressure inside, so choosing an extremely durable material was important.
The team started with a standard cross section and then modified it from there to help make movement within the cask concentric.
Testing Seals and Retainers on Site
Challenges with this project stemmed from lack of variability reduction in the manufacturing of these casks. Due to variations in each drum, fitting the seals was a challenge and required extensive testing to ensure the seals were inflating properly.
What’s unique about the installation of these seals is that they are used to hold in irradiated water within the casks, and then the casks are welded shut. We actually sent a team of engineers to the site of the nuclear reactor to help with testing and installation.
Why choose a fabric-reinforced seal?
There is so much pressure involved in circulating the water inside these casks that a fabric-reinforced seal was the only option. The fabric reinforcement inside the seal provides a kind of skeleton that makes the seal more rigid to survive a high-pressure environment. Putting fabric in the seal forces the cross-section to be restricted and not stretch, allowing for a thinner seal wall that can hold more pressure.
Need help with your project?
If you’re working on a project of your own and need to find the right solution, our engineering team can work with you to solve any problem.