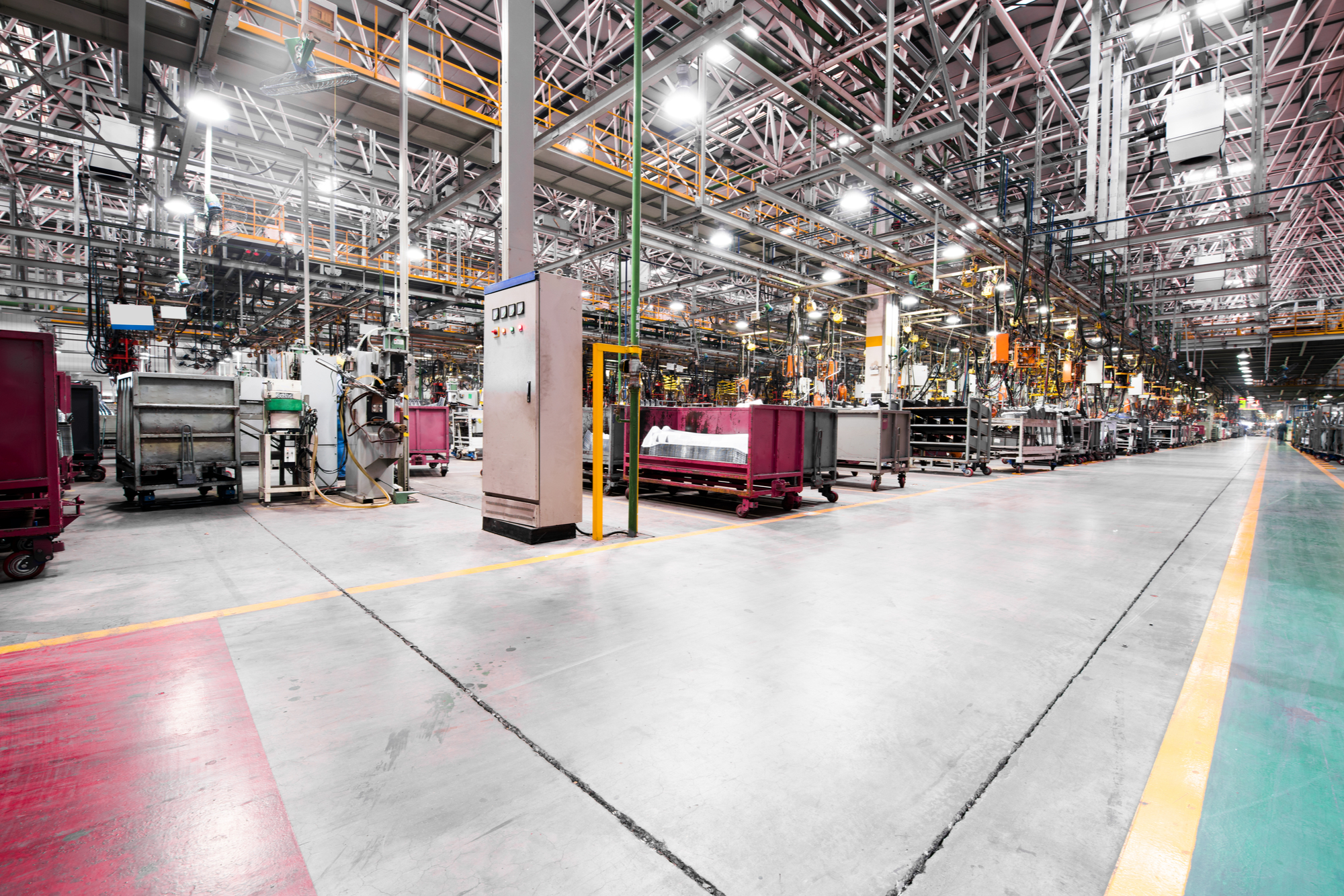
Inflatable Seals 101
Seal Master is an industry leader, creating custom engineered, fully molded, fabric reinforced inflatable seals and bags that are durable enough for intense industrial environments and applications.
Seal Master inflatable seals are fabric reinforced, fully molded, custom engineered rubber products that are created to provide solutions for a wide variety of applications.
To obtain the best results for your application, it is important to spend a few minutes exploring the features of Seal Master inflatable rubber seals, as well as defining the requirements of your application before completing our RFQ form.
What follows is a brief overview of the critical factors that impact the design of Seal Master inflatable seals. This information has been arranged to provide a step-by-step overview of the performance and design of Seal Master inflatable seals and how they can meet your application requirements. If you are already familiar with inflatable seals, feel free to explore individual topics of interest.
Geometry
Seal Master inflatable seals inflate and deflate in three basic directions of operation: the axial (or normal to the mounting plane) direction, the radial-in direction, and the radial-out direction. Each of these inflation directions has its own set of performance parameters for measurements, such as the height of inflation ("stroke" of the seal) and the centerline bend radius that the seal can negotiate.
These performance parameters are further impacted by the cross-section geometry of the seal.
Typical Inflatable Seal Configurations
There are as many different inflatable seal configurations (or cross-sections), as you can imagine.
Even though Seal Master Corporation has designed and created over 7,500 uniquely different products, it could be that the configuration that fits your application has not yet been created.
The configurations below have been created in response to a variety of industrial, research, and military requirements. The various cross-section geometry types each have specific performance parameters that permit them to function best in one or more of the inflation directions.
The inflatable seal profiles are further differentiated by the method by which they are retained.
Snap-In Type
Snap-in type inflatable seal profiles utilize a dovetail-designed base that enables the seal to simply "snap" into a matching retainer groove. The retainer groove provides support and protection for the seal. Installation and replacement is quick and easy.
Bond-In Type
Bond-in type inflatable seal profiles take advantage of an easily machined or fabricated straight-wall groove. This permits the seal to be positioned and bonded into place.
Encapsulated Type
The encapsulated inflatable seal profile allows for the seal to be "captured" in a groove by securing bar stock over the edges of the groove. The same effect is realized by trapping the seal in a specially formed channel. This approach employs an inflatable tube actuating a solid rubber shoe to the striking surface.
Fasten Type
The fasten-type inflatable seal represents a versatile system that utilizes a variety of metal fasteners such as bars, pins and clips, which can be tack welded or screwed down to the mounting surface.
Recessed Groove Type
The recessed grooved type inflatable seal, generally used with smaller diameter seals in a radially-in or radially-out mode, holds the seal in place by its own tension or force. When larger diameters are required, studs can be used.
Drop-In Type
This unique design, first used in the nuclear industry, does not require the help of extraneous "hold-down" or "hold-in" devices for retention. The seal is simply dropped into a groove or gap and is held in position by gravity and its own geometry.
Custom Inflatable Seals
These inflatable air seal profiles are only a representation of some of the typical profiles used and are not representative of all of the special profiles that have been created over our 40-year history. Seal Master inflatable seals are custom engineered and manufactured for your specific application and the profile is determined by the requirements of your application. Fill out our RFQ page with your unique requirements to get started on your inflatable seals project.
Define Your Application Geometry
Generally speaking, there are two major considerations that determine the seal profile for an application: geometry and environment. Consider the generic rubber seals profile above. Each of the labeled dimensions is defined by touching the cursor to the label.
Defining the geometry of your application means describing what you intend for the seal to do mechanically, and how you envision the seal's placement in the application. In other words, we need to know how much room there is in the application to mount the seal, and how far the seal will need to "stroke" to meet the striking surface.
A sketch/drawing of your application is very helpful for Seal Master Engineers to help determine the best inflatable seal approach for your application. Consider the generic seal profile above. Each of the labeled dimensions is defined by touching the cursor to the label.
Typical Air Connections
Air connections for Seal Master inflatable seals are integrally molded into the seal, thus providing the greatest strength and construction integrity.
Inflatable Seal Retaining System
Proper installation is essential to the function and longevity of an inflatable seal. A retainer must hold the seal in place, allow it the freedom to inflate and deflate, and protect it from damage. To facilitate the installation of our inflatable seals, Seal Master can provide metal, or elastomeric retainers in strip or circular form as illustrated below.
When required by the application, the rubber inflatable seal can be retained with a machined groove in your application as illustrated below:
Control Devices
Certain process applications require that the operation of the seal be specifically controlled or cycled. In this situation, a combination of control boxes, valves, regulators, gauges, alarms, and compressors may be required. Seal Master can provide a control device should your application require it.
The control device illustrated operates an inflatable seal used in an emergency rescue vehicle.
Application Environmental Considerations
The second major consideration that determines the best seal configuration for your application is the environment that the inflatable seal will experience. The environmental conditions will impact the materials (compound and fabric reinforcement) selected for the seal.
As you consider the environmental conditions the inflatable seal will experience in your application, recording them can be very helpful.
Construction & Materials
Seal Master seals are not simple rubber extrusions; they are custom built, fabric reinforced, and fully molded to fit your application. This ensures structural integrity for optimum performance.
Inflatable Seal Materials
Numerous combinations of fabric reinforcement and elastomers are utilized in Seal Master inflatable seal construction. These combinations are chosen in response to the geometric and environmental challenges of your application. You are not asked to specify materials to be used; this question is resolved through a collaborative effort between you and Seal Master engineers, as you define the performance parameters of your application.
Typical Elastomers Used in Inflatable Seals
Based on your environmental requirements, the best alternative elastomer will be selected.
- Butyl
- Chloroprene
- Epichlorohydrin
- Ethylene-Propylene
- Fluorinated Hydrocarbon (Viton®) Natural Rubber
- Nitrile (Buna N)
- Polyurethane
- Silicone
- Styrene-Butadiene (Buna S)
Fabrics Used in Inflatable Seals
Durability and shape retention is provided by a variety of fabrics; inflatable seals are reinforced for maximum strength. Typical fabrics used to reinforce Seal Master® inflatable seals include:
- Dacron
- Kevlar®
- Nomex®
- Nylon